Bladesmithing
Bladesmithing, to me, is the craft of creating the forged blade using the best tools and materials to make the finest knives possible. I have no objection to using the most modern tools I can afford, and yet many of the best tools for the job are the ones that a smith from hundreds of years ago would recognize immediately. This area of the site is dedicated to some of my favorite tools and some of the processes I use to make my knives.
I've always said that a valuable knife is one that tells a story. I have knives that belonged to my father and my grandfather, and they are priceless to me because they tell a story. My knives aren't produced by mindless machines run by bored workers, but one at a time in my shop by my eyes and my hands. Because of that, they come with a story built-in.
These tools tell a part of that story...

The anvil is the most basic of Bladesmithing tools. This is the only anvil I have ever bought, and still the only one I use. It is a JHM Competitor and weighs a massive 250 lbs. I bought it at a farrier supply shop when I was still living in California. It is a traditional pattern, cast steel anvil. Besides being a bear to move, it's a wonderful tool.

I don't own nearly as many hammers as you might think, and if I were doing ornamental blacksmith work, I'd have a lot more. But these are my two favorite. The larger one is a French pattern hammer that weighs a little over 4 lbs. The smaller one is a Hofi-style hammer and is about 3 lbs. Both hammers have slightly crowned squared faces and cross peens.
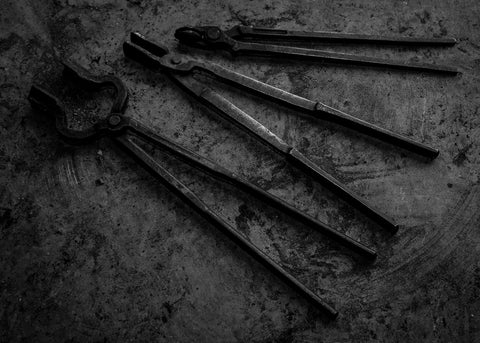
Good tongs are absolutely necessary to do good quality work because they allow you to hold onto hot steel securely and at the angle you need. For bladesmithing, I think these are my three favorite. The bottom pair is a set of V-bit tongs that work great for holding round or square stock, but especially flat bar stock (like a knife blade). I own several sizes of these same tongs. The middle pair is a pair I made. They are heavy duty, general purpose tongs. The top pair is the first pair of tongs I ever bought. I was learning to forge and was using vise grips to hold the steel. The blade worked loose and when I hit it, it flew up and hit me right above my right eye. So I ordered a good pair of tongs, in this case these cap-jaw tongs. They are versatile and I still use them constantly.

These are my two forges. The smaller one to the right was built by fellow knifemaker Len Landrum. It's a very small, efficient design that's perfect for forging a blade. The bigger one on the left is one of the many forges I've made. This one gets so hot I accidentally melted steel in it one time! It's forced air, with two burner ports. This is where Damascus steel and Laminated steel are born.

Air Hammer and Hydraulic Press. The Air hammer (foreground) is a tool I worked without for years, and when I finally got this one I wept for all the time I'd lost. These hammers have a lot of control, plenty of power for forging knife blades or making laminated steel. The hydraulic press behind it is the first power tool I built. It's over 15 years old now, and in need of a total retrofit. However, until time permits it still presses on (terrible pun) and has been responsible for making hundreds of pounds of Damascus and Laminated steel.

Files. Another thing you can't have too many of. After all these years and with all the bigger and more precise tools I have, there are still jobs which can be done best with a good file.

Bill Moran is credited with coming up with the idea for a knife vise made from two pieces of pipe. I'd only seen a picture of one once, and one day over lunch I described it to my dad. From that, he went home and made this up for me. One adjustment screw (with a link of chain welded on as a handle) holds the knife, one allows me to rotate it to any angle, and the other lets it swivel left or right. That was over 15 years ago, and there is not a knife I have ever made that has not spend a good deal of time in this vise. Thanks, Dad.

Grinders. I've always said, if it weren't for good grinders I'd never be able to make a living as a bladesmith. These are my two KMG Grinders, one variable speed, one a high-speed model. Multiple tooling arms are interchangeable and give these machines a lot of versatility.

This is my Bridgeport Mill, made in the mid-1960's. Back when tools were made to last, machines including this one were responsible for making anything - everything - that this country needed in war and in peace. Too many of these have ended up in scrapyards as machinists were replaced with computers. This one still runs on electricity and elbow grease.

This is my main leather workbench. I use a heavy granite surface plate for tooling and working leather, while behind it are stamping and carving tools, many of which I've made, along with a lot of other assorted tools. I used to despise working with leather. It's a very strange medium. If wood and clay got together and had a child, it would be leather. It stretches, it stains, and it absorbs water. And yet, without those qualities, I'd never be able to make sheaths the way I do. In time I did grow to love working with it, and it's now one of the things I enjoy most about being a bladesmith.